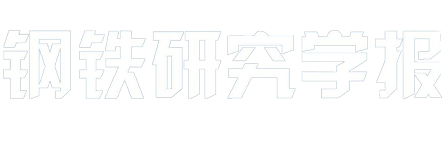
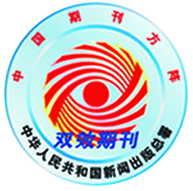
ISSN 1001-0963
CN 11-2133/TF
中国钢铁工业协会 主管
中国钢研科技集团有限公司 主办
CN 11-2133/TF
中国钢铁工业协会 主管
中国钢研科技集团有限公司 主办
电液伺服疲劳试验机优化控制初探
Preparatory Study on Optimal Control of ElectroHydraulic Fatigue Testing Machine
{{custom_ref.label}} |
{{custom_citation.content}}
{{custom_citation.annotation}}
|
/
〈 |
|
〉 |