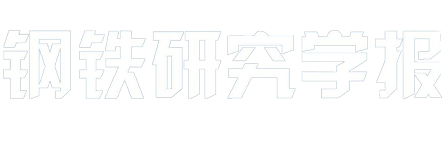
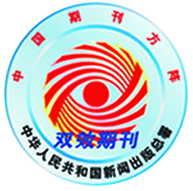
ISSN 1001-0963
CN 11-2133/TF
中国钢铁工业协会 主管
中国钢研科技集团有限公司 主办
CN 11-2133/TF
中国钢铁工业协会 主管
中国钢研科技集团有限公司 主办
Numerical Analysis of Interfacial Heat Transfer Coefficient During Large Steel Ingot Solidification
LAN Peng,,ZHANG Jia-quan,
Journal of Iron and Steel Research ›› 2014, Vol. 26 ›› Issue (8) : 29-36.
Numerical Analysis of Interfacial Heat Transfer Coefficient During Large Steel Ingot Solidification
steel ingot / interfacial heat transfer coefficient / inverse model / numerical simulation {{custom_keyword}} /
/
〈 |
|
〉 |