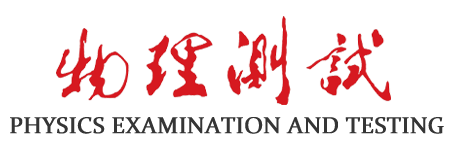
ISSN 1001-0777
CN 11-2119/O4
中国钢铁工业协会 主管
中国钢研科技集团有限公司 主办
CN 11-2119/O4
中国钢铁工业协会 主管
中国钢研科技集团有限公司 主办
Analysis of the low temperature Charpy impact of 4330 forgings
HA Yao,CHEN Chang-hua,ZHANG Long-qun,ZOU Jun,QIAN Jian-qing
Physics Examination and Testing ›› 2019, Vol. 37 ›› Issue (1) : 24-28.
Analysis of the low temperature Charpy impact of 4330 forgings
charpy impact / metallography / scanning electron microscopy / intergranular fracture {{custom_keyword}} /
/
〈 |
|
〉 |