Welcome to visit Iron and Steel, July 24, 2025
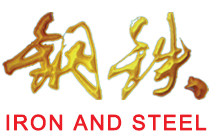
- “中国科技期刊卓越行动计划二期”中文领军期刊
- 中国精品科技期刊顶尖学术论文(F5000)
- 《科技期刊世界影响力指数(WJCI)报告》
- 《冶金工程技术与金属材料(金属学与金属工艺)
- 领域科技期刊分级目录》T1级别
- 中文核心期刊
- 中国科技核心期刊
- 中国科学引文数据库来源期刊
- 中文科技期刊数据库收录期刊
- 中国学术期刊文摘收录期刊
- EI数据库收录期刊
- SCOPUS数据库收录期刊
- 美国《金属文摘》收录期刊
- 美国《剑桥科学文摘》收录期刊
- 美国《化学文摘》收录期刊
- 日本科学技术文献速报收录期刊